This article is an excerpt from the new book, Tesla: How Elon Musk and Company Made Electric Cars Cool, and Remade the Automotive and Energy Industries, by Charles Morris.
The five co-founders of Tesla—Marc Tarpenning, Martin Eberhard, Elon Musk, JB Straubel and Ian Wright—were certainly greenies, and the environmental value of EVs was one of their prime motivators. However, they were also rocket scientists and sports car connoisseurs, and they were well aware of another exciting advantage of electric powertrains. Unlike a dinosaur-burning engine, an electric motor delivers maximum torque from the moment you step on the pedal, delivering performance that not even the most exclusive of gas-powered sports cars can match.
Tom Gage and Paul Carosa, working for a company called AC Propulsion, had taken full advantage of this instant torque to build the tzero, a car that had a magic power: anyone who drove it instantly changed their opinion of electric cars. This was the rock that Musk and his Musketeers planned to build their company on. The Tesla team made a deal with AC Propulsion to license its motor and inverter technology, and started work on what would become the revolutionary Roadster.
The tzero’s performance was impressive, but as the Tesla team worked with it, they found that there was a lot of room for improvement. JB Straubel and his team of engineers ended up redesigning almost every part.
“AC Propulsion had produced 60 drivetrains or something like that, all hand-crafted,” Marc Tarpenning told me. “Each motor was matched with each inverter and they were all hand-tuned. This is not manufacturing, this is high-end hobbyist. We [licensed their motor] and we realized they couldn’t manufacture it, so we just designed our own motor which, in the end, was quite a bit different from what we started with.”
According to Tarpenning, the Tesla team moved on from AC Propulsion’s motor pretty early in the game. “We redesigned it a year before we were in production. We did need one for the mule [the first test vehicle]. But that was long before we were even into the engineering prototypes, let alone the validation prototypes, which then lead into production.”
The AC Propulsion guys, who didn’t get to ride the Tesla rocket to fame and fortune, remember things a little differently. Paul Carosa told me that Tesla “stopped paying royalties halfway through the Roadster production, claiming that they were no longer using our technology, which was not clear. If you look at the Roadster motor and the power modules, it’s essentially our technology there. I don’t think the relationship ended on a good note.”
Tom Gage: “I think they paid a license for the first five hundred vehicles, and then there was a change in design which they claimed eliminated their reliance on our licensed technology. There was never any real discussion of what they had changed. It was hardball, but that’s the way they do things in the auto industry.”
The way that the patents and the contract were written, it would have been difficult to prove that Tesla did anything wrong, and AC Propulsion didn’t want to get into a legal battle. “After all was said and done, our patent wasn’t as clear as it should’ve been,” said Gage. “So, [a lawsuit] would’ve made the lawyers rich but probably nobody else.”
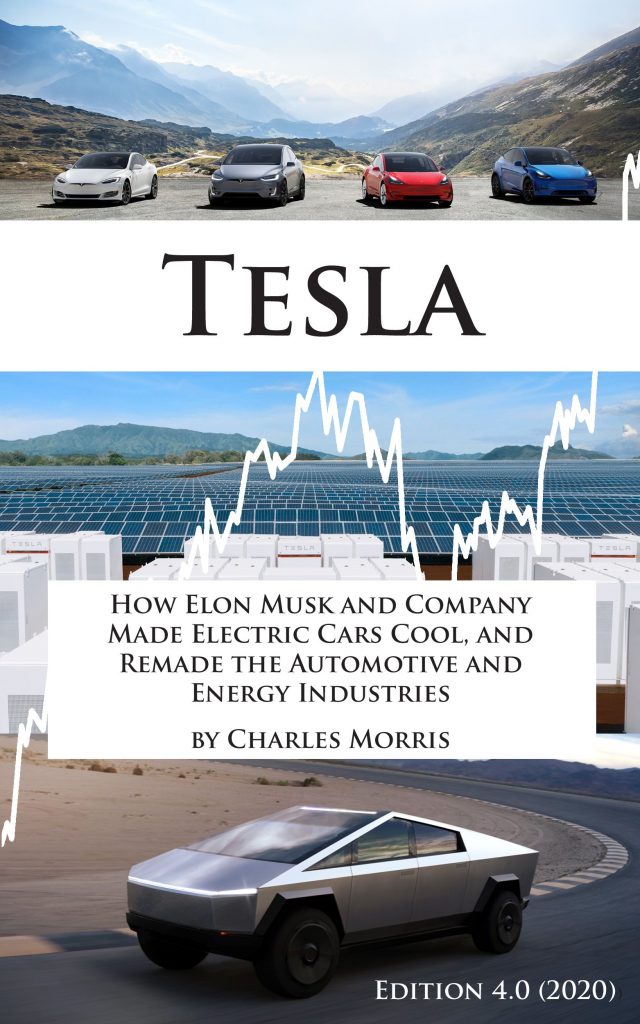
“To this day, there’s still a fair amount of our DNA in the Tesla design, which is not to say they haven’t made huge progress and improvements,” said Gage. “But AC Propulsion was really a very significant jumping-off point for Tesla in all of the basic propulsion and battery system efforts that they pursued. They got a pretty good deal from AC Propulsion.”
THE BATTERIES
When Tom Gage and his team built the second generation of the tzero, they were able to make a huge improvement by taking advantage of a new technology that was just becoming commercially available. In fact, this was the key technology that made the current generation of EVs possible—the lithium-ion battery.
The original tzero used 1,000 pounds worth of lead-acid batteries. These delivered fine performance, but the weight and volume of all those batteries seriously limited the practicality of the vehicle.
In 1991, the first lithium-ion batteries came on the market. Lithium-ion technology offers much better energy density (the amount of energy that can be stored for a given volume) than the century-old lead-acid design, and EV pioneers like Gage and Eberhard immediately saw the potential. By replacing the original tzero’s lead-acid batteries with lithium-ion cells, they were able to more than triple the car’s range. There was never any question for the Tesla team that lithium-ion batteries were the way to go for the Roadster’s battery pack (which Tesla referred to as the Energy Storage System, or ESS).
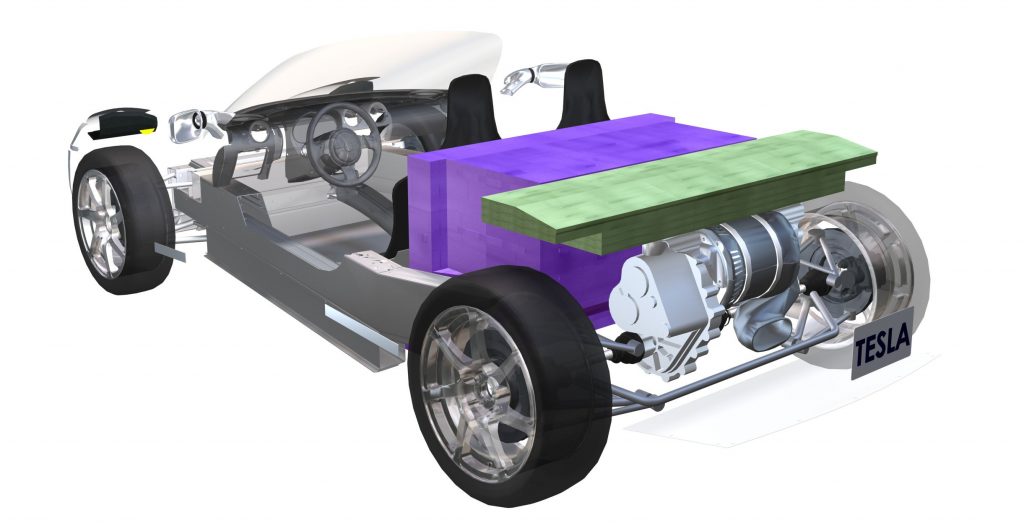
The idea of using the laptop-style (Panasonic 18650) lithium-ion cells was a “great minds think alike” moment. Neither the AC Propulsion guys nor the Eberhard/Tarpenning team claimed the inspiration—all told me that both teams were already working with the idea when they joined forces.
Marc Tarpenning oversaw the engineering of the Roadster’s battery system. “A battery system, almost like a disc drive, has lots of different parts. It has mechanical components, and there’s a lot of mechanical engineering involved and safety as well, both mechanical and electrical. Then, there’s a whole bunch of computers, fourteen computers in a battery pack. So, my world is really about the computers, the software and the firmware.”
As Tarpenning recalls, the second-generation tzero was “sort of our proof of concept that this could work, that lithium-ion cells were the right way to go—these little 18650s, which we had used in e-books,” said Tarpenning.” (Before starting Tesla, Tarpenning and Eberhard had built an early e-book at a startup called NuvoMedia.) “You had to be careful with them because they were a lot more finicky to work with, but their energy density was so much better that it would be ridiculous not to spend a little bit of engineering time to work with them, and they kept getting better. Every time we looked around, they were another 7% better or 7% cheaper. They were kind of in a slow Moore’s Law.”
ELISE + TZERO + SPECIAL SAUCE = ROADSTER
The tzero was basically a proof-of-concept vehicle, an electric powertrain installed in a basic kit car, and the powertrain was really the only part that the Tesla team was interested in. They meant to assemble a car that excelled in every detail, so for several of the puzzle pieces, they turned to a company that they all admired—Lotus.
Some have written that the Roadster was “based on” the Lotus Elise, but this is a vast oversimplification. In fact, the two cars share around six percent of their components. The Roadster incorporated a lot of styling and other elements from Lotus, and some of the powertrain of the tzero, but Tesla made so many modifications and improvements to almost every part that it really was a new vehicle.
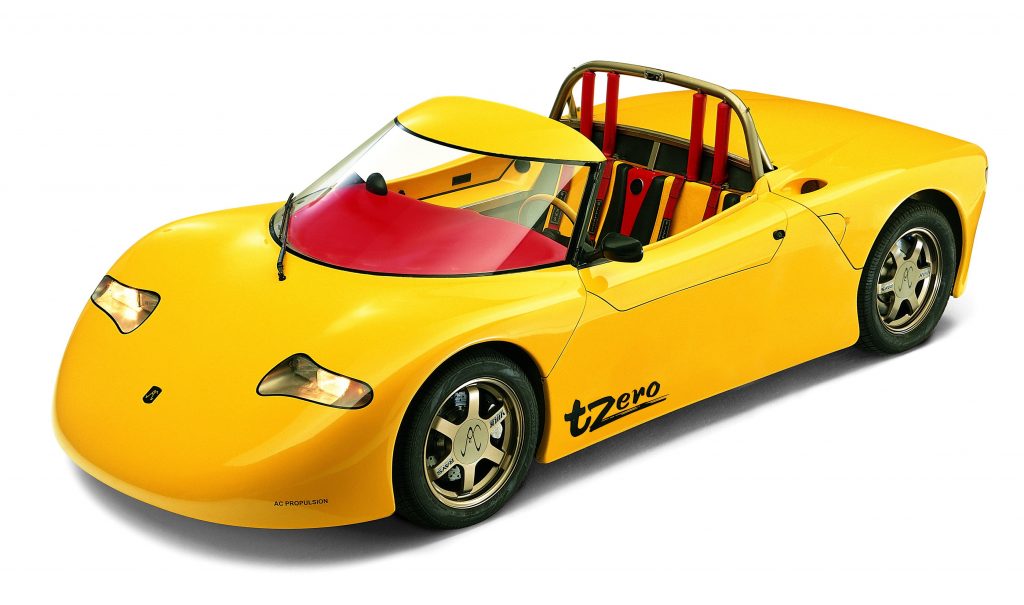
Tesla licensed various technologies from Lotus, and contracted with the automaker to manufacture the cars in its legendary factory, with Tesla supplying most of the parts.
The Tesla team redesigned the Elise’s chassis in several ways. They lowered the height of the door sills by two inches, making it easier for tall chaps like Musk and Eberhard to get in and out. They also rearranged the layout, making the wheelbase about two inches longer to accommodate the battery, and made several other revisions and improvements.
In early 2005, Lotus provided a couple of glider versions of the Elise. A glider is a car with no engine or transmission, and the Tesla team would use these to test their electric powertrain. When the boys installed their electrified innards into the glider, they had themselves a mule, which is a working car that can be driven to test various components on the road (according to Marc Tarpenning, it’s called a mule because, like the equine animal, it doesn’t reproduce).
“To get a car onto the road from scratch, it costs hundreds and hundreds of millions of dollars,” Tarpenning told me. “Our whole business plan was based on the fact that we weren’t going to do that—we were going to develop a drivetrain and then we were going to take a design that had already passed the crash and safety tests both in Europe and America.
We knew we could make an AC induction motor. The battery system was something that was scary. We wanted to get rid of that risk as soon as we could. So we worked on the battery system first and we made a Lotus Elise into a mule, using our first-generation battery pack, an AC Propulsion inverter and an AC Propulsion motor. We drove that around, and that allowed us to get more people interested and to raise more money. It validated that the battery system was going to be okay, we were going to have a couple hundred miles of range and it was going to be really fun to drive.”
Lotus provided the airbag system and ABS brake system, components that would have been very difficult for Tesla to develop on its own. This is why the Roadster’s steering wheel and dashboard look pretty much like the Elise’s. Most of the rest of the interior is all Tesla. The Californians also used the Elise’s windshield and other windows (called the greenhouse or glasshouse in the trade). To roll their own would have meant dealing with a host of related issues including visibility requirements, rollover protection, waterproofing, windshield wipers and more.
For the body, the boys decided to use the best material available—carbon fiber composite (aka carbon fiber reinforced plastic or CFRP). As strong as steel, as light as aluminum, and more flexible to work with than either, this space-age stuff might be the ultimate material for automobile exteriors. It still isn’t cheap, and in 2004, deciding to use it was a bold move. (For its post-Roadster models, Tesla elected not to use CFRP, because of the cost.)
Once the decision was made to use carbon fiber, the team was no longer building a modified Elise, but a completely new car, and they had the freedom to design the body however they wanted.
THE STYLING
People who aren’t “into cars” might be amazed to learn how much effort automakers devote to a model’s physical appearance. The Founding Fathers, however, were very much car guys, and they wisely spent a lot of time and money on getting the Roadster’s styling just right. Indeed, one of the things that bothered Eberhard about the fuel-efficient models he saw on the road was the fact that they looked so square and unexciting. Make no mistake, people perceived the Roadster as a different animal from previous EVs not only because of its performance, but also because of its looks.
Once the team had figured out what the overall dimensions of the Roadster would be, they engaged several renowned sports car designers to submit proposals for its styling. Martin Eberhard had a clear vision in his mind of how he wanted the car to look, and he tried to explain his ideas to the stylists. Apparently, however, they were all thinking in terms of a stereotypical “electric car,” and the first designs that came back looked like cheesy space vehicles, complete with solar panels and other science-fictionesque gizmos—precisely the opposite of what Eberhard and company wanted.
Eberhard’s next call was to his friend Bill Moggridge, a London-born “designer’s designer” who designed the first laptop computer, and co-founded the design studio IDEO. Moggridge created a scheme that described the appearance of a car in terms of five separate characteristics, each of which was presented as a continuum with an example car at each end—for example, from masculine to feminine, from retro to ultramodern, etc. Eberhard then chose a point along each axis that represented where he imagined the look of the Roadster. They showed this to the designers working on the project, and the next round of proposals was much more in line with what Eberhard and his team had in mind.
Dozens of sketches from the designers were hung on the walls of a room at Eberhard’s house, and over 50 people were invited to vote for their favorites. Barney Hatt, a member of the Lotus Design Studio, emerged as the clear winner. Over the next few months, Eberhard and the others worked closely with Hatt, tweaking every detail of the new car’s styling. Elon Musk was also deeply involved in the details of the design—among other things, he insisted on developing custom headlights, which was an expensive process, but had a lot to do with the impressive appearance of the Roadster’s front end.
Much remained to be done before the Roadster hit the road. The development of any new car involves extensive testing of all the major components and systems, which requires building all sorts of models, prototypes and pre-production vehicles. For Tesla, which obviously didn’t have the vast complex of labs and shops that a major automaker has, all this required some ingenious improvisation and more than a little help from their friends at Lotus.
By January 2006, Tesla had built a second drivable mule, and was assembling the first engineering prototype. Between then and early 2007, Tesla built ten of these (EP1 through EP10), which were continually taken apart and reassembled to test various components. Once all the pieces of the puzzle were more or less perfected, the company built 26 validation prototypes (VP1 through VP26), beginning in March 2007. These were almost-final versions of the automobile, and were used for endurance and crash testing.
THE ROADSTER HITS THE ROAD
Tesla made automotive history on July 19, 2006, when it officially unveiled the first electric car of the modern era for an audience of 350 invited guests in a hangar at Santa Monica Airport. The cars on display were actually the first two engineering prototypes, EP1 and EP2. The new stars also posed for the cameras at the San Francisco International Auto Show in November, where Governor Arnold Schwarzenegger highlighted the Roadster in a speech. “Every industry has to participate in the fight against global warming, and these clean, efficient alternative fuel vehicles are leading this environmental revolution,” said the Governator. “I test drove this vehicle, and it is hot.”
The Roadster is truly a world car. The carbon fiber body panels came from the French firm Sotira. The brakes and airbags were made by Siemens in Germany, and the chassis and much of the suspension were built by Lotus in the UK. The Roadster’s final single-speed gearbox was made in Auburn Hills, Michigan by BorgWarner. For Roadsters destined for sale in North America, Lotus sent the chassis to Menlo Park, California, where Tesla employees installed the powertrain. Cars bound for customers in Europe and elsewhere were assembled at the Lotus plant in the UK.
TRANSMISSION TROUBLES
By the end of 2007, the testing was done, the global supply chain was in place, a million other details had been taken care of, and everyone was itching to start producing cars. Tesla was already shifting into delivery mode when a major problem came up.
Straubel and the engineering team originally designed the Roadster with a two-speed manual transmission. An electric motor, unlike an internal combustion engine, has the most torque at low RPMs and is quite efficient at all speeds, so an electric vehicle doesn’t really need a multi-speed transmission. Most have only a simple reduction gear, and no traditional transmission at all. In fact, this is one of the big advantages of the EV. Fewer gears means fewer moving parts, less energy lost to friction, and lower maintenance costs. Seamless acceleration, with no pauses to shift gears, means a smoother driving experience.
However, unlike previous EVs, the Roadster was designed for performance—the green motorheads of Tesla were determined that it be able to reach 60 mph in under four seconds, and have a top speed of 125 mph. Given the powertrain that Straubel and his team of engineers were working with, it wasn’t possible to achieve both the sub-four-second acceleration and the 125 mph top speed with a single-speed transmission, so they used a two-speed design, with second gear designed to kick in above 60 mph.
At the last minute, just as Tesla was getting ready to start assembling cars, the team realized that the transmission wasn’t cutting it, and production ground to a halt. Actually, the tranny worked fine, but it wouldn’t last. Apparently, the high torque and high RPMs of the electric motor were burning the transmissions up at about 3,000 miles.
Tesla missed the advertised date for its first deliveries, and the press pounced. As Motor Trend put it, the Roadster was “beginning to look like vaporware, and the traditional auto industry was sniggering.” The boys from California would have to improvise a solution at highway speed.
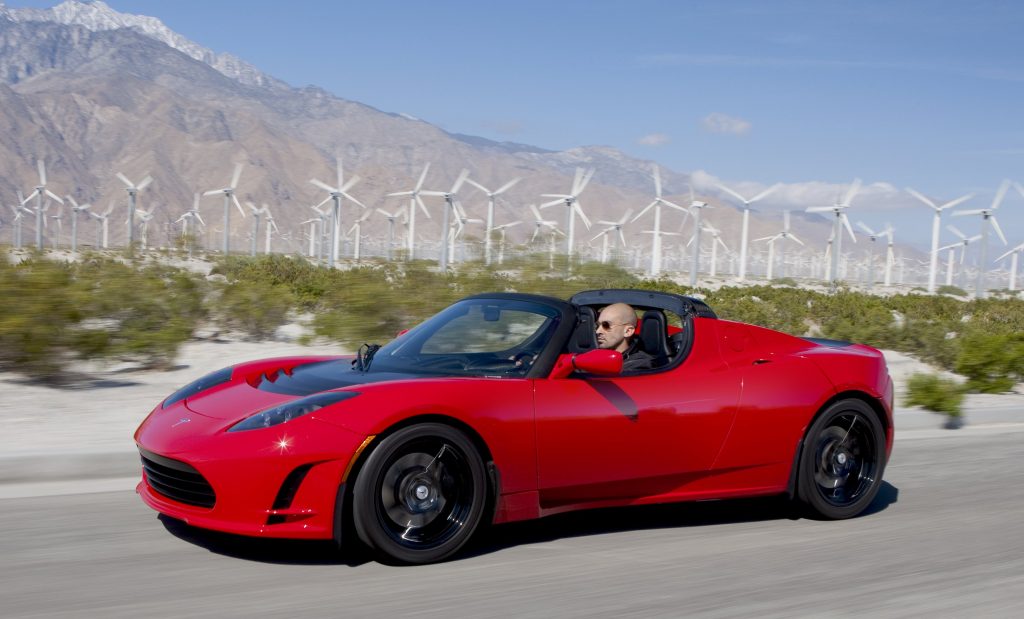
Tesla announced that it would start shipping Roadsters with the transmissions locked into second gear, meaning that they would only be able to accelerate from 0 to 60 in 5.7 seconds (not Porsche territory, but not exactly pokey either). As soon as it developed and validated a new transmission, it would retrofit the cars with the new units at no cost to the owners.
Tesla brought in the engineering consulting firm Ricardo, which had developed the transmissions for the Bugatti Veyron, Ford GT and other high-performance vehicles. After experimenting with several different designs, the company developed a brand-new single-speed transmission—essentially just a reduction gear. While the new system, which the company called DriveTrain 1.5, went through the months-long validation process, Tesla announced it would begin series production of Roadsters in March 2008 with the interim single-speed transmission, to be retrofitted with the new transmission later.
In the end, as they had done with the motor controller (and, symbolically, with the entire auto industry), Straubel and his engineering team leveraged digital technology to not only eliminate the transmission problems, but to make major improvements. As Tarpenning put it, they were “rescued by Moore’s Law.” Improved transistor technology allowed them to increase the performance of the inverter and give the motor more efficiency and more torque. This in turn enabled the simpler single-speed gearbox to deliver the coveted sub-four-second blast of acceleration. It also just happened to improve the car’s range by ten percent, to 244 miles.
Tesla selected automotive supplier BorgWarner to manufacture the new gearbox, and started slowly ramping up production of the Roadster. In line with Tesla’s Master Plan, as production volume went up, the cost of building each unit went down—and none too soon. Shortly before production began, the company did a study that predicted that building each Roadster would cost about $120,000. This turned out to be way too low—in the end, the materials alone cost $140,000 per car. With a base price of $92,000, Tesla was losing money on each unit, an unsustainable situation that caused the burn rate to soar, and tempers in the boardroom to boil over. For the 2009 model, the company raised the price to $109,000 to try to cover some of the costs. Fortunately, sales steadily trickled in, and costs came down as increased scale allowed suppliers to reduce costs and lessons learned on the production line led to more efficiency. By June 2009, the cost of materials had come down to $80,000 per car, and the cost and revenue curves came together just in time.
Once the transmission troubles and some early quality control issues were sorted out, things went remarkably smoothly. The press reaction to the Roadster was spectacular, and the car and the company soon began grabbing headlines. However, Tesla’s problems weren’t over—the global financial crisis took its toll, and growing tensions between Musk and Eberhard led to a period of turmoil and instability. Nonetheless, Tesla pressed ahead with the next step in its Master Plan—the development of Model S.
===
You’ve just read an excerpt from Chapter 5 of the new book, Tesla: How Elon Musk and Company Made Electric Cars Cool, and Remade the Automotive and Energy Industries, by Charles Morris. Subsequent chapters explain how the company built on its success with the Roadster to develop even more ground-breaking electric vehicles. The latest edition brings the Tesla story all the way up to the present day—it includes detailed assessments of Model Y from Tesla expert Roger Pressman and manufacturing guru Sandy Munro, as well as a description of plans for the Tesla Semi and Cybertruck.
Original Publication by Charles Morris at EVANNEX.
Want to buy a Tesla Model 3, Model Y, Model S, or Model X? Feel free to use my referral code to get some free Supercharging miles with your purchase: http://ts.la/guanyu3423
You can also get a $100 discount on Tesla Solar with that code. No pressure.