Tesla’s Battery Day detailed a number of topics related to the future of efficiencies in cell manufacturing. The presentation, however, also showed how the automaker is improving the design of its vehicles using a modern battery architecture. Inside its vehicles, Tesla aims to follow the same strategy to boost the mass, range, and structural integrity of its vehicles.
It’s been reported earlier this year that a single-piece casting method on the Model Y will be used by Tesla. The improved casting removes 79 parts per vehicle, which not only improves production performance, but also improves driver safety. Thanks to the casting, which is achieved by a giant machine known as the Giga Press, the cost of each vehicle’s rear underbody design also decreases by 40 percent.
The one-piece rear casting is manufactured from Tesla’s own aluminum high-pressure alloy that has a high strength due to no heat treatment or coatings that would remove the structural integrity of the design. After manufacturing, heat treating a casting of this size causes deformation, said CEO Elon Musk during the event.
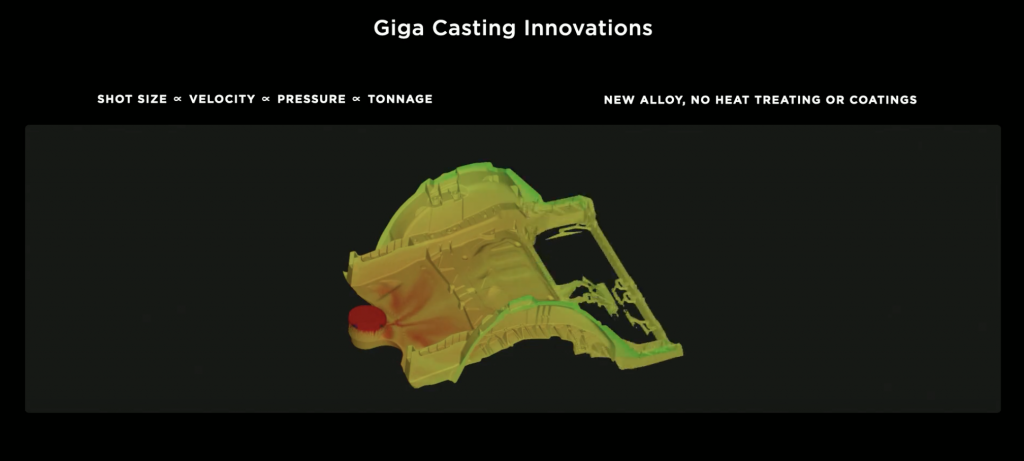
The design team at Tesla, however, also drew inspiration from aircraft wings to enhance the structural integrity of their vehicles. While the casting increases production efficiency and strength, structural battery placement removes excess structure from the battery packs, raising density.
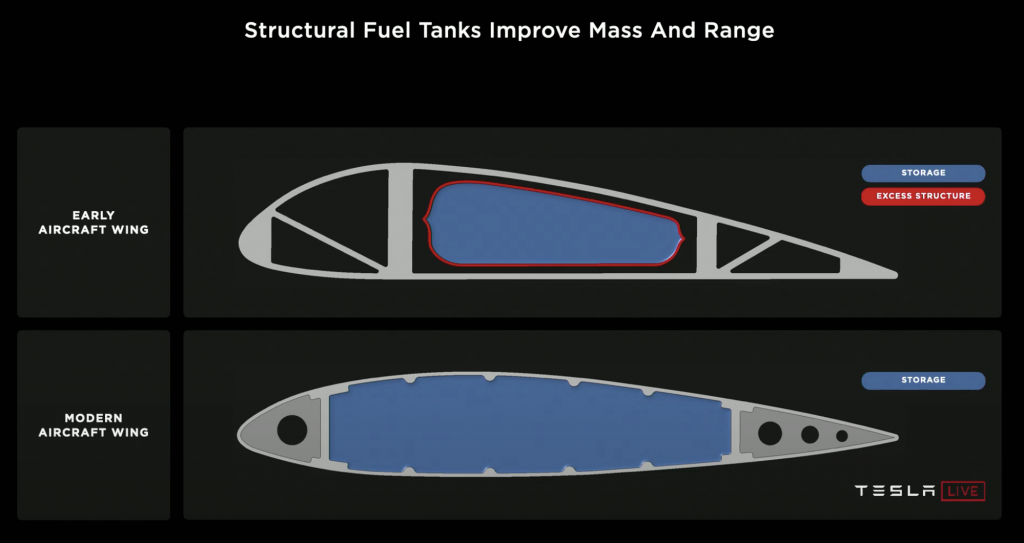
“The non-cell portion of the battery has negative mass,” Musk said. “We saved more mass in the rest of the vehicle than in the non-cell portion of the battery. So how do you really minimize the mass of the battery? Make it negative.”
The negative mass minimization allowed the automaker to increase the battery pack density. Due to the eradication of unnecessary structures within the pack itself, individual cells may be placed more effectively. The new Tesla battery design is absolutely free of any negative mass, which along with structural integrity increases pack density.
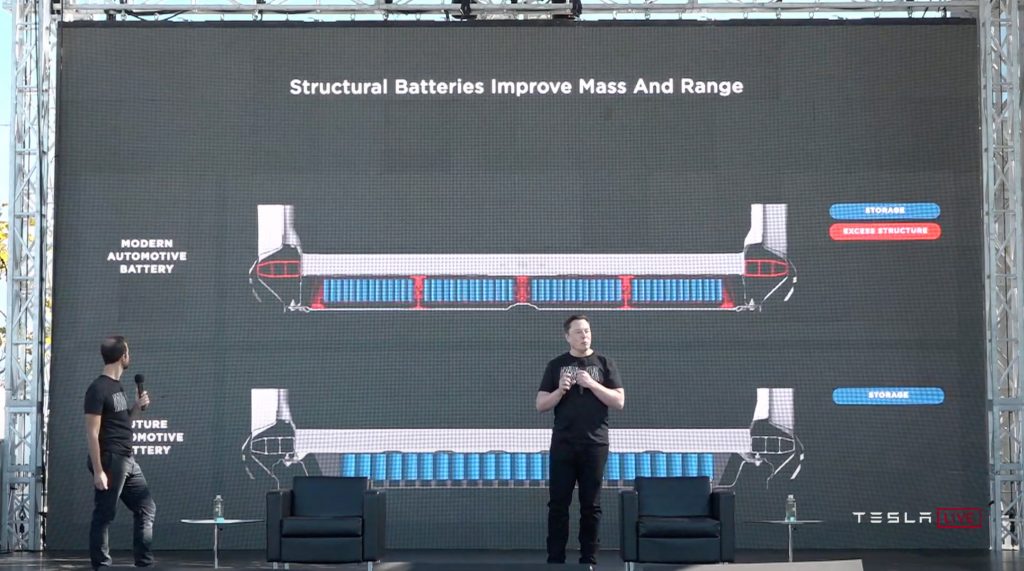
“The pack itself is structural,” Musk stated.
In addition, the filler that currently uses a flame retardant inside the Model 3 and Model Y packs now uses a structural adhesive and flame retardant. This adhesive binds the cells to the top and bottom sheets of the pack efficiently. “This allows you to do sheer transfer between the upper and lower sheet,” which in the case of a crash increases stiffness and avoids severe deformation.
Improvements in the casting design of the future Tesla cars and the newly built battery architecture, which uses new materials and stiffness-enhancing techniques, will increase the already safe vehicles manufactured by the company. With the Model S, Model 3, and Model X, Tesla already holds three different five-star crash safety scores. The Model Y has not yet been tested, but the vehicle already uses the one-piece rear casting system at the Fremont production facility.
Tesla Battery Day was no disappointment. While the blueprint for cell production efficiency was laid out, the company also demonstrated how the structure and architecture of the battery could improve the safety of Tesla’s vehicles. The new design revolutionizes EVs as a whole and will potentially contribute to more safety than previously seen.
Want to buy a Tesla Model 3, Model Y, Model S, or Model X? Feel free to use my referral code to get some free Supercharging miles with your purchase: http://ts.la/guanyu3423
You can also get a $100 discount on Tesla Solar with that code. Let’s help accelerate the advent of a sustainable future.