“Large-scale manufacturing, especially if it’s a new invention, is somehow between 1,000 and 10,000% times harder than a prototype.” — Elon Musk
In this article, I will try to explain why.
Most people you ask on the street (or at a conference) about a new invention will tell you the invention and the first prototype are the hardest part, and manufacturing it afterward is just a question of capital and resources. Nothing could be more wrong and detached from reality.
Like many kids in cities do not really know where milk comes from (possibly from the grocery store?), a similar number of people do not know where products come from that they use every day. Most have never seen a production facility from the inside. It’s more likely they saw a video in which the production lines ran and looked perfect, smooth, clean, and easy. In reality, production lines for new products usually stand still, because something routinely does not work as it’s supposed to.
The key invention after an invention is the invention of how to mass manufacture it. If you don’t master that, your invention is worthless.
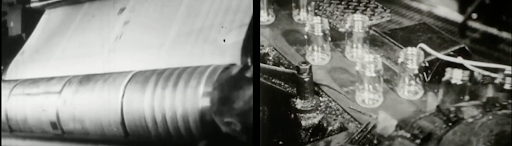
People talk about the moment when an inventor had their moment of truth when she or he found the unique technology, chemical, or physical solution that was without a doubt an enlightening moment of wisdom and joy. What they don’t talk about is why most inventions never make it into production and into the hands of consumers, and why if they do at all, it’s usually decades later. Most inventions wait so long to somehow be reproduced in volume that they have been forgotten, and that’s the reason why most inventions have been invented again and again and again.
How is that possible? The answer is because it’s 1,000% to 10,000% harder to mass manufacture a new invention than to build a prototype.
A new invention that you present to the public with a prototype is usually handmade, sort of a piece of art. It’s a unique piece, and although you can, of course, hire more skilled people who make copies, that will remain very expensive and therefore not affordable for the masses. It does not scale. Equally important, it will not have a harmonized quality and its specifications will vary too much. In the world of batteries, you need them to be like “one-egg twins,” with 100% the same DNA all the time. Otherwise, there’s a high risk your battery pack will fail.
Every single piece may work on its own but is slightly different, and the pieces that don’t work according to required specifications may be many, or I should say too many. All of this makes production expensive, and makes your product unaffordable. If people cannot afford it because it’s more a piece of art than a mass-produced product, then it’s literally a worthless invention. The world is full of worthless inventions that look great on paper and even as prototypes, and you can even maybe produce them in small volume, but not enough to be successful at mass production. The world is full of forgotten inventions no one talks about anymore (forgotten 2,000 year old Roman inventions, for example).
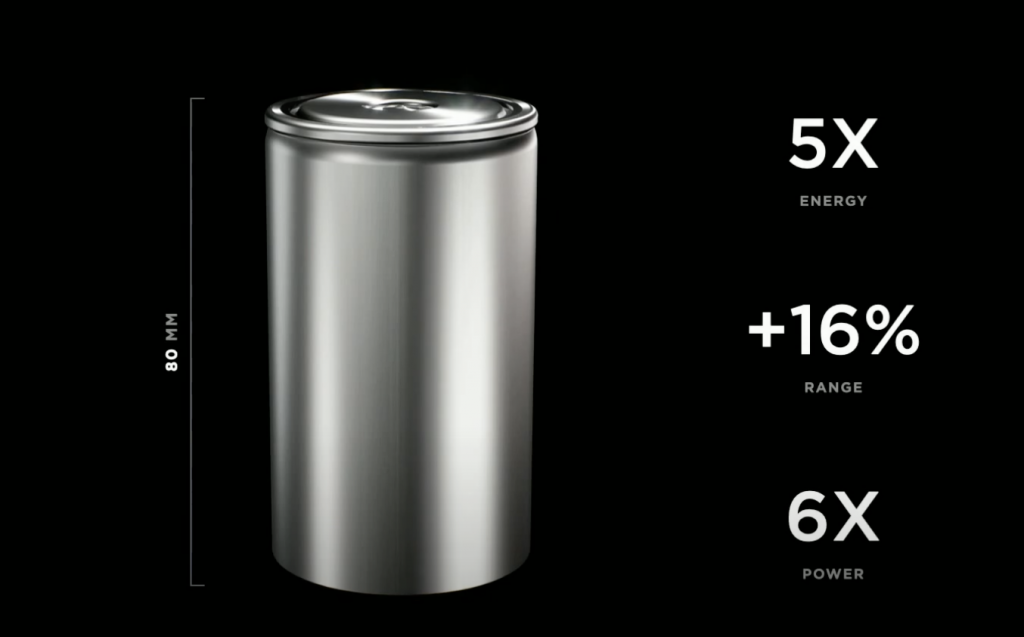
An invention that is worth something is one that can be manufactured in high volume for a low cost per unit and within defined quality parameters and specifications. The majority of inventions in the world never passed that test and disappeared either until being forever forgotten or until manufacturing and material science developed to a required level.
Manufacturing is underappreciated, underrated, often called magic, and done in hidden places most people have never seen. Wherever you are in this very moment, look around yourself and identify the products you use that were once invented, and ask yourself if you know how they are produced today. Even if you really wanted to know how they were produced, you probably wouldn’t get access to the production facilities.
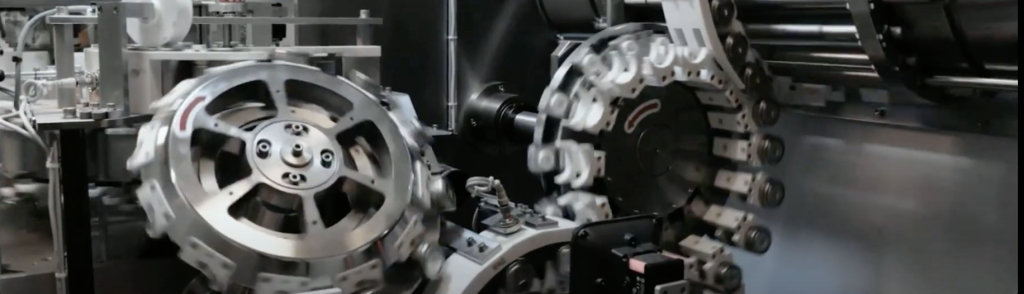
When I was in Fremont, California, last week, I was right in front of the production facilities of the new Tesla battery line and died to step in, but, unfortunately, because of covid-19 safety rules, no access was granted. One day, I will have the opportunity to see the most advanced Tesla gigafactory and its battery production, and I am dreaming of that day.
The issue with an invention is that, to bring it to market, you need to invent also how it’s manufactured. All other products around you have manufacturing facilities that have been built, improved, and made perfect with small changes and improvements over years or decades. A truly new innovation like the tabless battery from Tesla needs a lot of innovation in terms of how to manufacture it. Otherwise, it will never make it into a battery electric vehicle, house battery, or utility battery storage system.
When Elon Musk and Drew Baglino talked about how hard it is and how long it will take to mass produce their new invention, they talked about the invention of mass manufacturing within defined quality criteria and technical specifications and not that it is hard to produce a few units. That has been completely misunderstood by almost everybody, and frankly, it drove me mad to hear all the confusion of people not understanding anything but talking out loud as if they did. They could have at least been quiet, recognizing that it’s not their field of expertise. Instead, they spread confusion and wrong thoughts.
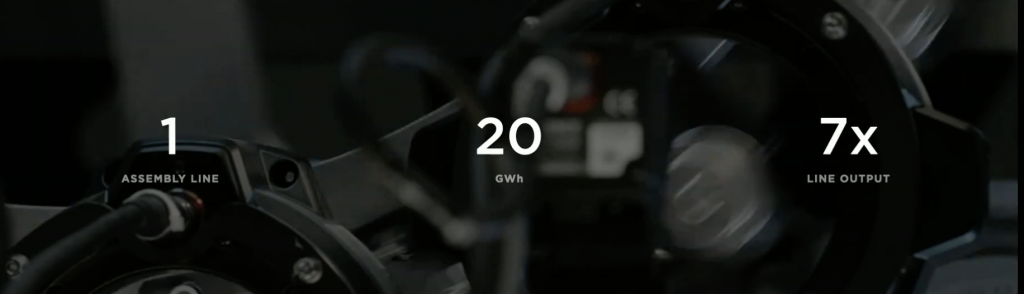
In particular, batteries have very small tolerances to comply with technical requirements to last long enough with many charging cycles and in different working conditions. To reduce that risk, Tesla many years ago started to work with battery modules to manage that risk and to be able to exchange complete modules if needed — as you could not take out just one faulty battery cell without destroying the pack in the process. Today, with the new battery architecture, modules will be a part of the past, which makes the requirements for perfect mass manufacturing of each cell even more demanding and a hard requirement.
All of that needs to be taken into account when you invent a mass production system that, like on the German Autobahn, should flow with high speed like water in a fast river, with no traffic jams, no stop-and-go traffic, and no unexpected accidents. The spice needs to flow.
Imagine you have an endless line of cars driving on the German Autobahn with no speed limit and they drive 150 mph (240 km/h) with a short distance between each other. On their right and left side, they have service vehicles going the same speed and assembling vehicle parts, connecting units together, filling the air in wheels, loading software, and doing other complex tasks at the same speed, but only for parts of a second until they switch to the next vehicle. They remain all the time at the same spot on the Autobahn. These cars are our batteries and the service vehicles are the tools on the production line that work on them.
And now imagine something unexpected happens and a car hits something on the road at 150 mph. The disaster starts and we have a massive mass accident with damage done not only to the vehicles but also the service cars, their tools, and of course the Autobahn itself. A large group of emergency and repair vehicles, like ambulances, car carriers, police, cleaners, and other repair service units are alarmed, drive to the location, and repair and clean everything until the Autobahn is free to use again. The traffic jam is incredibly long and everybody is in a bad mood, while the root cause of that accident is not yet determined and analyzed. The faster and closer the vehicles go, the larger the damage that is done and the time lost. You are going through an endless sequence of mass accidents, and each improvement you implement is a change that causes new ones somewhere else. The line is standing still most of the time.
Now, smart people come in and try to find out how this could happen and what needs to be changed to avoid such a disastrous mass accident again. To find the root cause is work like Sherlock Homes does. A solution can be a small tool adjustment, a material change, or a buffer increase with no certain outcome for success, because it never has been done before.
Trial and error is necessary. Simulating what may happen can only help to a certain degree. Trial and error is occurring often — even if a stable production process is known and underway, it needs to be continuously calibrated, adjusted, changed, and optimized in an attempt to achieve the perfect speed and orchestration of tools, products, and conditions. All of that is a true art, and the fun part is the artists are people no one ever applauds or even knows.
Every little stop in rapid mass production is a cost, and a quality disaster, as the process requires a constant flow of material at a certain speed for good quality. While all the batteries are quickly moving over the line, tools modify them and work on them on the fly, and if just one little millisecond goes wrong for some reason, the damage and costs created are exponential. A slight temperature change, a human hair, or an incorrect cleaning material can cause the next disaster mass accident on our Autobahn. The higher the production rate is — and Tesla aims to make it so fast that your eyes won’t be able to follow the moving objects — the smaller a deviation needs to be to create a process break that can be expensive in retooling but also in repair and lost time.
But if you get it right and the process flows seamlessly, like a hot knife goes through butter, you have managed to create the invention no one will talk about but that is at least as important as the invented product itself.
Elon tried to explain in an adorable way and with a lot of effort, and with help from Drew, what they have invented and why mass manufacturing is hard. Still, the average audience did not listen nor understand it. I can feel the pain. In my business life, I was in the same role of explaining complex technical matters — be they about technology, data analytics, or supply chain management challenges. All of them are dynamic challenges, while we humans have a DNA that mostly understands static issues. That’s why most people aim at the puck where it is and not where it will be.
The hardest problem, though, is not even lack of education or base understanding. The hardest problem is sending and receiving information between humans. Regardless of how hard you try and how well you explain a complex matter, what you send will never be received if the receiving element is not open or willing to receive it.
Battery technology and mass manufacturing sound complex, but they are not rocket science that you need to study for years to understand. Everyone can comprehend the basics with common sense if you really want to.
Analysts and media covering the Battery Day event did not want to receive what Elon sent, and that’s a pattern I’ve watched for years. We saw the same at Autonomy Day and at other events. Unfortunately, I don’t see that changing in the future.
Speaking for the audience I hope to represent, we are all incredibly grateful that Tesla made the effort to explain to us what was, in my opinion, a historic inflection point in battery technology that will, without a doubt, pave the path to a sustainable future.
While I share the frustration, Elon hopefully understands that the effort was very well received by the people who wanted to receive it.
Postscript: Why do I qualify to talk about manufacturing anyhow?
I grew up as a kid in a manufacturing environment in which my family discussed process adjustments and productivity improvements during practically every lunch. As a grown-up, I worked in production myself and later as an engineer with a degree in production technology. I spent the majority of my life running around manufacturing facilities for days trying to understand and give advice regarding technological processes and mass production improvements. It’s kind of a part of my DNA now.
Original Publication by Alex Voigt at CleanTechnica.
Want to buy a Tesla Model 3, Model Y, Model S, or Model X? Feel free to use my referral code to get some free Supercharging miles with your purchase: http://ts.la/guanyu3423
You can also get a $100 discount on Tesla Solar with that code. Let’s help accelerate the advent of a sustainable future.