About a year ago, Tesla effectively shocked the electric vehicle industry by announcing that the Made-in-China Model 3 Standard Range Plus would be using lithium iron phosphate (LFP) batteries produced by Contemporary Amperex Technology (CATL). It seemed like an unprecedented decision, considering the company’s image as a maker of fast, powerful, premium cars.
LFP batteries are cheaper to produce than NCM (nickel-cobalt-manganese) and NCA (nickel-cobalt-aluminum) batteries, but they generally have lower energy density. This meant that usually, vehicles equipped with LFP cells end up lacking in range and charging. Tesla’s move towards LFP could then be considered a gamble–one that could have resulted in drawbacks for the Model 3 in China.
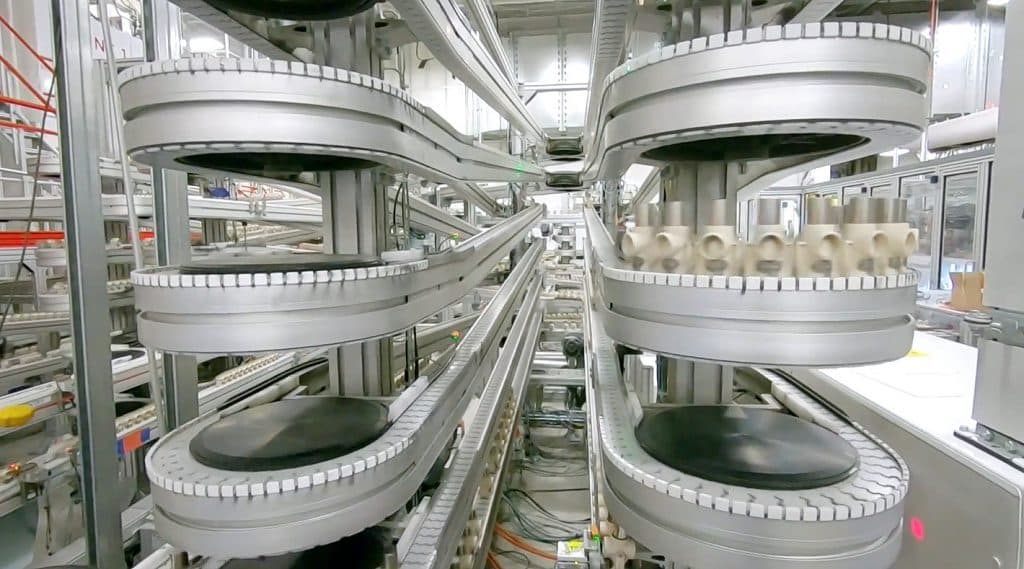
Today, it seems safe to say that the Silicon Valley-based electric car maker’s gamble has been successful. Recent tweets from Elon Musk even point to the idea that LFP is the way to go for Tesla’s standard range vehicles. This was especially notable, considering that cobalt and nickel prices have been rising over the past years. And with the advent of more electric cars in the market, securing more long-term supply for raw materials is incredibly important.
True to form, Tesla’s adoption of LFP batteries was immediately felt by the greater battery market. As noted in a Mining.com report, the 55KWh LFP-battery Tesla Model 3 from China captured 5.9% of the global full electric car market in terms of battery capacity in its second full month of sales. This was despite the Made-in-China Model 3 not being sold in the United States.
Based on Adamas Intelligence data, the momentum of Tesla’s LFP-equipped Model 3 only increased from that point. Propelled further by deliveries to Europe, the LFP-battery China-made sedan comprised 46% of all Model 3 sales in January and a remarkable 32% of the battery capacity in all LFP-equipped cars globally. This trend, Adamas’ data showed, boosted LFP’s overall share in the global battery market in terms of capacity to 18.5% in January 2021.
This was a remarkable milestone for LFP batteries, considering that it only commanded 1% at the beginning of last year and 3% by June 2020. Adamas Intelligence’s Head of Data and Analytics Alla Kolesnikova noted that the momentum of LFP cells had been particularly felt in China. In 2020, the adoption of the cobalt-free batteries saw a resurgence in the market, with both veteran automakers and younger EV companies adopting the technology.
“LFP battery capacity deployed onto roads increased six-fold and we continue to see cathode manufacturers ramping up output and a growing list of the automakers in China announcing upcoming model-versions that will incorporate LFP cells. Among the more prominent are Xpeng, Seres, and VW,” Kolesnikova said.
Roskill, one of the world’s first management consultancies and a key player in critical materials supply chain intelligence, has determined that LFP cathode and precursor material manufacturing capacity is currently up 10-fold in January-February 2021 compared to the same months in 2020. A good part of this is the adoption of the batteries by notable EV players like Tesla, as well as breakthroughs in the cobalt-free batteries themselves.
Roskill analyst Kevin Gunan Shang noted that LFP batteries are looking to be an excellent fit for cell-to-pack manufacturing, which would be adopted by Tesla for its mass-market vehicles like the Model Y. The analyst also pointed to the claims of Volkswagen-backed Chinese battery manufacturer Gotion, which noted that its latest LFP battery had achieved a cell-level energy density of 210 Wh/kg, putting it on par with NCM 523.