JB Straubel, formerly the chief technology officer for Tesla, is now the head of a new company called Redwood Materials whose principal business will be recapturing the lithium, nickel, cobalt, and other valuable components inside lithium ion battery cells and using them to make new batteries. In a recent interview with the Wall Street Journal, Straubel said raw materials constitute as much as 75% of the total cost lithium ion batteries.
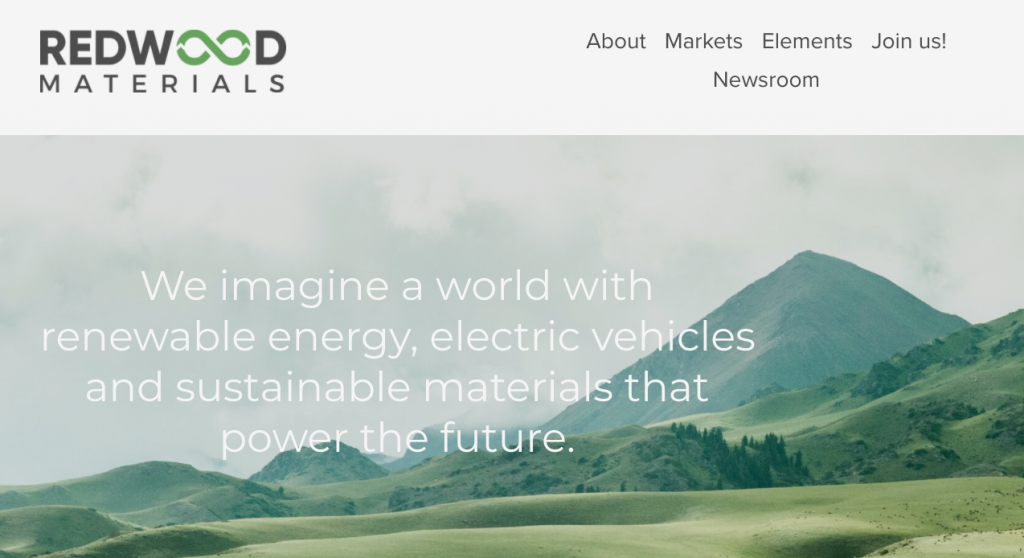
Recycled materials will be less expensive than mining, refining, and transporting new materials, which means recapturing and reusing them will drive down the cost of batteries. That in turn will further accelerate the EV revolution by making electric cars less expensive. Straubel foresees a process so efficient that nearly 100% of the valuable components of discarded batteries could be recaptured and reused.
“We need to really appreciate that we need to build a Gigafactory in reverse,” Straubel told the WSJ. “I’m looking into the future and seeing this freight train coming at us.” His vision is not just about recycling battery cells. Simon Moores, managing director of Benchmark Mineral Intelligence, says even in the best run factories there is a scrappage rate of 10%. He predicts that by 2025 manufacturers could be making up to 800 GWh of batteries annually. If so, there could be as much as 80 GWh of scrappage a year — equal to total global battery production in 2016. And that’s before a single used EV or energy storage battery gets recycled. Straubel’s suggestion of an onrushing freight train is entirely apt.
Moores foresees the following amounts of raw materials being recaptured annually by 2025:
- 64,000 tons of lithium
- 96,000 tons of graphite
- 45,000 tons of nickel
- 18,000 tons of cobalt
- 22,000 tons of manganese
He says those materials could have a market value of up to $1.5 billion, depending on commodities prices, which tend to fluctuate substantially over time. “Forever the entire market has been dictated by the commodity price of these metals,” Straubel says. “This is a chance to change that whole equation and to realize material cost savings in a way that short-circuits that industry.”
The Redwood Materials Mission
On its website, Redwood Materials lays out its raison d’être as follows: “Invent sustainable materials to build the world.” It adds, “Humanity has made great leaps forward in sustainable energy generation and transportation. We have invented and proliferated electronic devices to every corner of the globe and lifted billions of people out of poverty and into the information age. As these trends grow and mature, we at Redwood are planning ahead to address the problems and opportunities coming when millions of EV’s batteries need an end of life solution and when the electronics piled up in your drawers at home find a new life.
“We have an appreciation for the incredible scale of materials involved in the transition of the whole world to sustainable energy and we know it is not too early to plan for “un-manufacturing” the many Gigawatt-hours of batteries being built today. And we know that inventing circular supply chains, turning waste into profit and solving the environmental impacts of new products before they happen…..…will save our planet.”
The Panasonic/Tesla Connection
In its 2019 Impact Report, Tesla said it had begun its own in-house battery recycling program to recover lithium, cobalt, aluminum, copper, and steel from used batteries at Gigafactory 1 in Nevada. “While fossil fuels are extracted and used once, the materials in a lithium ion battery are recyclable,” the report said. “When petroleum is pumped out of the ground, chemically refined and then burned, it releases harmful emissions into the atmosphere that are not recovered for reuse. Battery materials, in contrast, are refined and put into a cell, and will still remain at the end of their life, when they can be recycled to recover its valuable materials for reuse over and over again.”
“The closed-loop battery recycling process at Gigafactory 1 presents a compelling solution to move energy supply away from the fossil-fuel based practice of take, make and burn, to a more circular model of recycling end-of-life batteries. From an economic perspective, we expect to recognize significant savings over the long term, as the costs associated with large-scale battery material recovery and recycling will be far lower than purchasing and transporting new materials.”
Panasonic, which manufactures batteries at the Gigafactory, is now working with Redwood Materials as the two companies assess how they can create a long term recycling program. According to Inside EVs, in late 2019 Panasonic began a trial with Redwood Materials to reclaim more than 400 pounds of the scrap from it battery manufacturing process at the Gigafactory and has now increased that to 2 tons. All of the scrap coming from its side of the Nevada battery facility is now shipped to Redwood. Celina Mikolajczak, a vice president at Panasonic Energy of North America and a former Tesla employee says Straubel’s “process looks like it’s way more sustainable from an environmental perspective.”
Other Battery Recycling Projects In The Works
Redwood Materials is far from the only company concerned with recycling batteries. The Chinese government now requires all battery manufacturers to have recycling programs in place. EV Obsession reports that KIA and SK Innovation have entered into a new partnership that will focus on battery recycling and battery development for future electric cars. Northvolt and Norway’s Hydro are designing recycling protocols for batteries and electric motors. Audi and Umicore are doing much the same thing.

In the bad old days, used tires got discarded in massive piles in the woods, old lead acid batteries were simply buried in land fills, and worn out cars were left to rust in fields. Today, such profligate ways are seen as economically unsound, as the notion of a circular economy gains wider acceptance. As Redwood Materials points out, we can’t afford to just throw away our old junk any more. There’s treasure in those discarded items. The push to find ways to reuse the raw materials inside lithium ion batteries is a recognition that the Earth’s resources are finite and should be conserved, not squandered. Perhaps there is hope for humanity yet?
Original Publication by Steve Hanley at CleanTechnica.
Want to buy a Tesla Model 3, Model Y, Model S, or Model X? Feel free to use my referral code to get some free Supercharging miles with your purchase: http://ts.la/guanyu3423
You can also get a $100 discount on Tesla Solar with that code. Let’s help accelerate the advent of a sustainable future.