In what is probably a sign of things to come for SpaceX’s nascent Florida Starship factory, the company’s original Starbase facility in South Texas may be about to graduate from tents to more permanent buildings.
More than two years ago, in late 2019, SpaceX followed in the footsteps of Tesla and began constructing a surprisingly advanced factory out of a series of tents. Instead of Model 3s, though, SpaceX would be building and assembling sections of the largest and most powerful rocket ever built. Measuring approximately 120 meters (~390 ft) tall, 9 meters (~30 ft) wide, ~5000 tons (~11M lb) fully fueled, and capable of producing around 7500 tons (~16.5M lbf) of thrust at liftoff, Starship is a fully reusable rocket that aims to perfect what SpaceX has already achieved with partially reusable Falcon 9s and Heavies.
Nonetheless, Starship manufacturing represents a substantial departure from the methods SpaceX uses to build Falcon rockets.
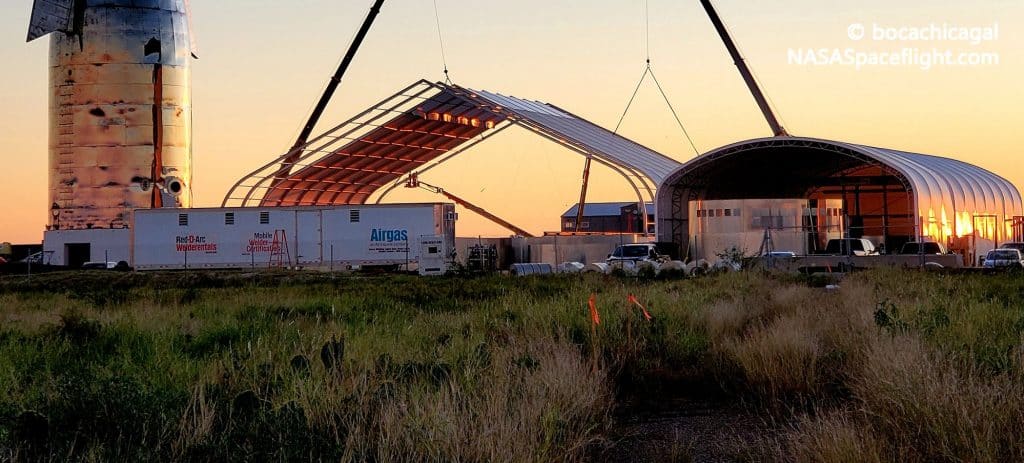
Instead of heavily leaning on horizontal integration (meaning that the rockets are primarily assembled in a horizontal orientation), Starship and its Super Heavy booster are almost exclusively assembled vertically. Excluding the machining of major loadbearing structures, Starship manufacturing generally begins with giant rolls of thin (3-4mm or ~0.15 in) stainless steel. SpaceX uses a custom tool to unspool the sheet metal, cuts off a roughly 28-meter (~92 ft) long strip, and then welds the ends of that strip together to produce a cylindrical barrel. Repeat that process 57 times and you end up with enough rings to assemble a full Super Heavy booster and most of a Starship.
However, using increasingly custom tools, SpaceX first stacks and welds those individual rings together to form sections of two, three, four, or five. Each section is then prepared for its specific role with a range of cutouts, plumbing, reinforcements (vertical stringers or circumferential stiffeners), thrust structures (the plates that Raptor engines attach to), and other add-ons. Most importantly, certain stacks of rings are mated with large steel domes – welded together out of prefabricated steel plates – to form forward, common, and aft dome sections. For Starship, SpaceX also assembles the ship’s conical nose section in a similar manner.
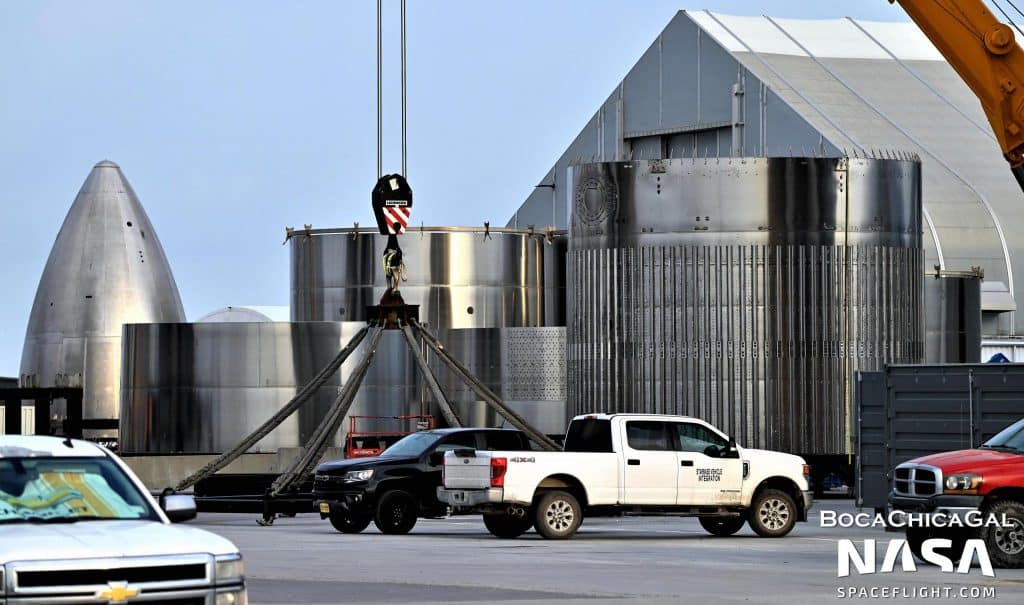
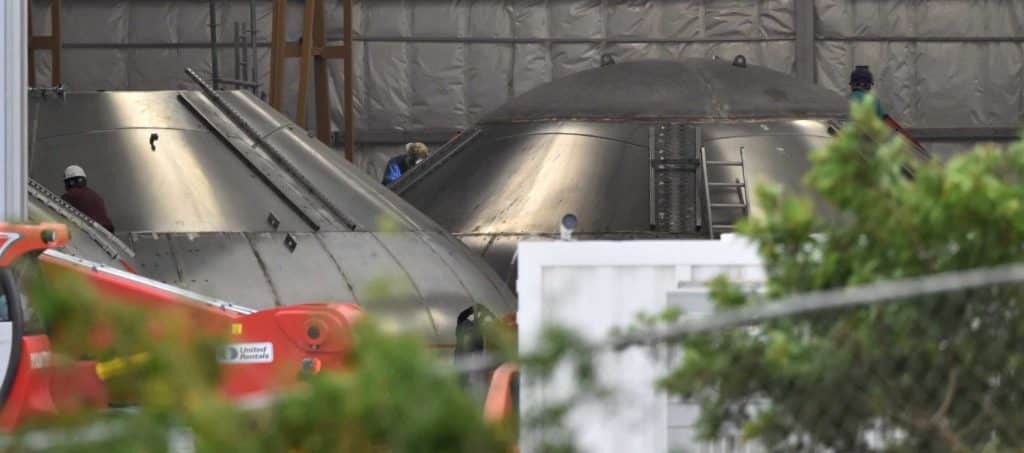
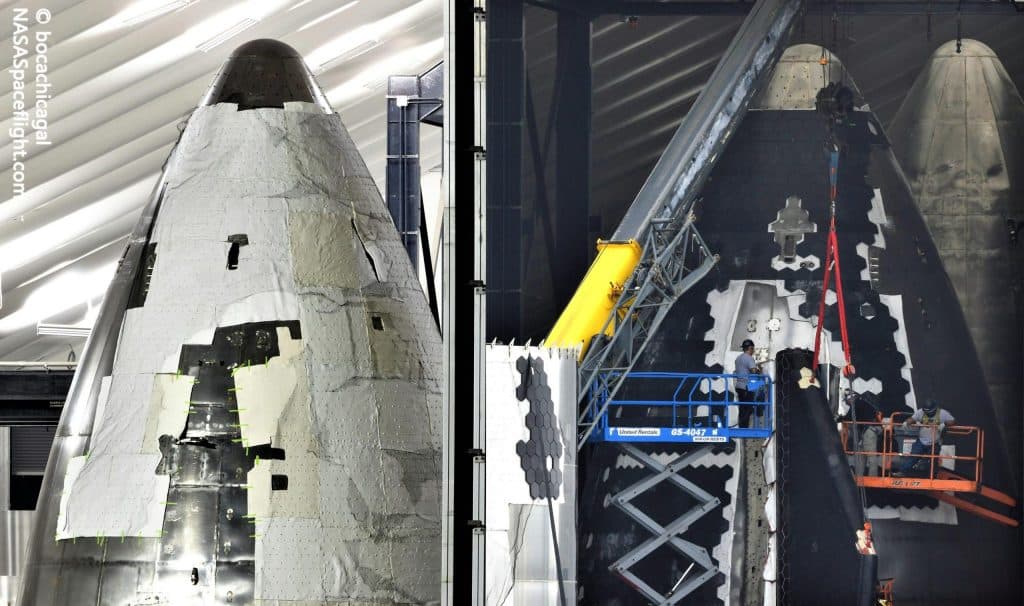
Virtually all ring, dome, and nose assembly work is conducted in one of three massive tents – each about 114m x 35m (375′ x 110′) – that form the backbone of Starbase’s Starship factory. Finally, SpaceX has built a series of massive open-air bays where, once fully outfitted, each ship and booster section is stacked in a specific order and welded together to complete the basic structures of Starship and Super Heavy.
While SpaceX continues to speed towards the completion of Starbase’s largest and tallest Starship assembly bay yet, the latest news centers around Starbase’s tents. After physically relocating a smaller but still substantial tent believed to be used basic metalwork (laser/water cutting, presses, etc.), SpaceX has rapidly broken ground and partially completed the foundation of a massive, new building believed to be the start of an upgraded Starship factory.
According to RGV Aerial Photography, SpaceX isn’t merely expanding the main three-tent factory with a fourth larger, permanent building. Instead, it reportedly aims to replace all of Starbase’s tents with a single 300,000-square-foot (~28,000 square meter) building that will be about 18 meters (60 ft) tall and likely measure around 800 feet (250m) long and 400 feet (120m) wide. Starbase’s tents are roughly the same height but their tented roofs mean that only a fraction of that height can be used for ring work and only a fraction of the floor space for taller nose work.
In comparison, a 300,000 square-foot building would have almost two and half times as much covered floor space as Starbase’s three tents – all of which can theoretically be used for ring and nose section assembly. In fact, with a mostly flat 18-meter roof, SpaceX could feasibly expand most ‘stacks’ by a ring or two, which would reduce the number of sections (and thus stacking operations) needed to assemble a ship or booster.
All told, while tents (“sprung structures”) can clearly be indefinite solutions for things like automotive manufacturing, Starship production is one case in which a more permanent flat-ceiling building is undeniably superior. With more than two years of experience and data to draw from, SpaceX may finally be confident enough in its present-day Starship production methods to commit to the construction of Starbase’s next evolution. Stay tuned to see where it leads.